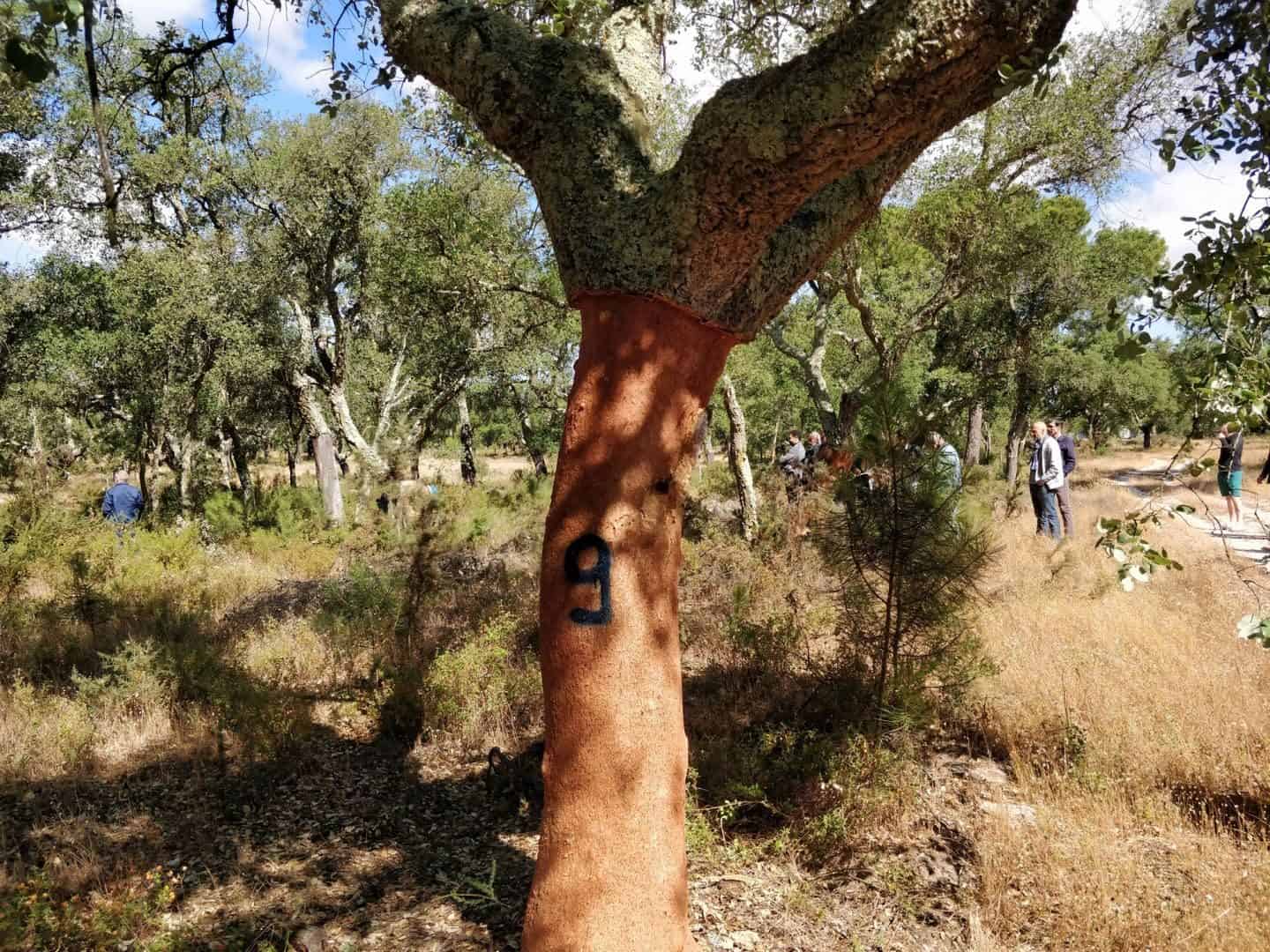
I have had an ongoing love affair with cork for a number of years now. It dates back to about 2012 when I wrote this article for Freshome. This was pretty much the time when I started to notice a lot of products, other than wine stoppers, being made from cork and, after looking into it for that article, I became aware of what an amazing material cork is. I have since bought quite a few cork products for my own home and I decided a few years back as we were updating the kitchen that I would quite like cork flooring.
It had always been a dream of mine to visit Portugal to see the cork being harvested but I had no idea how I could organise this. It took me all of about five seconds to accept when The Colour Flooring Company asked me if I would like to accompany them on a trip to Lisbon and Porto to see the harvesting and visit the factory where their cork flooring is made.
Prior to this, I thought that The Colour Flooring Company only did rubber flooring, but I discovered that they also supply vinyl, cork and a new generation of ultra-green sheet flooring called Okofloor which is made from organic castor and rapeseed oils.
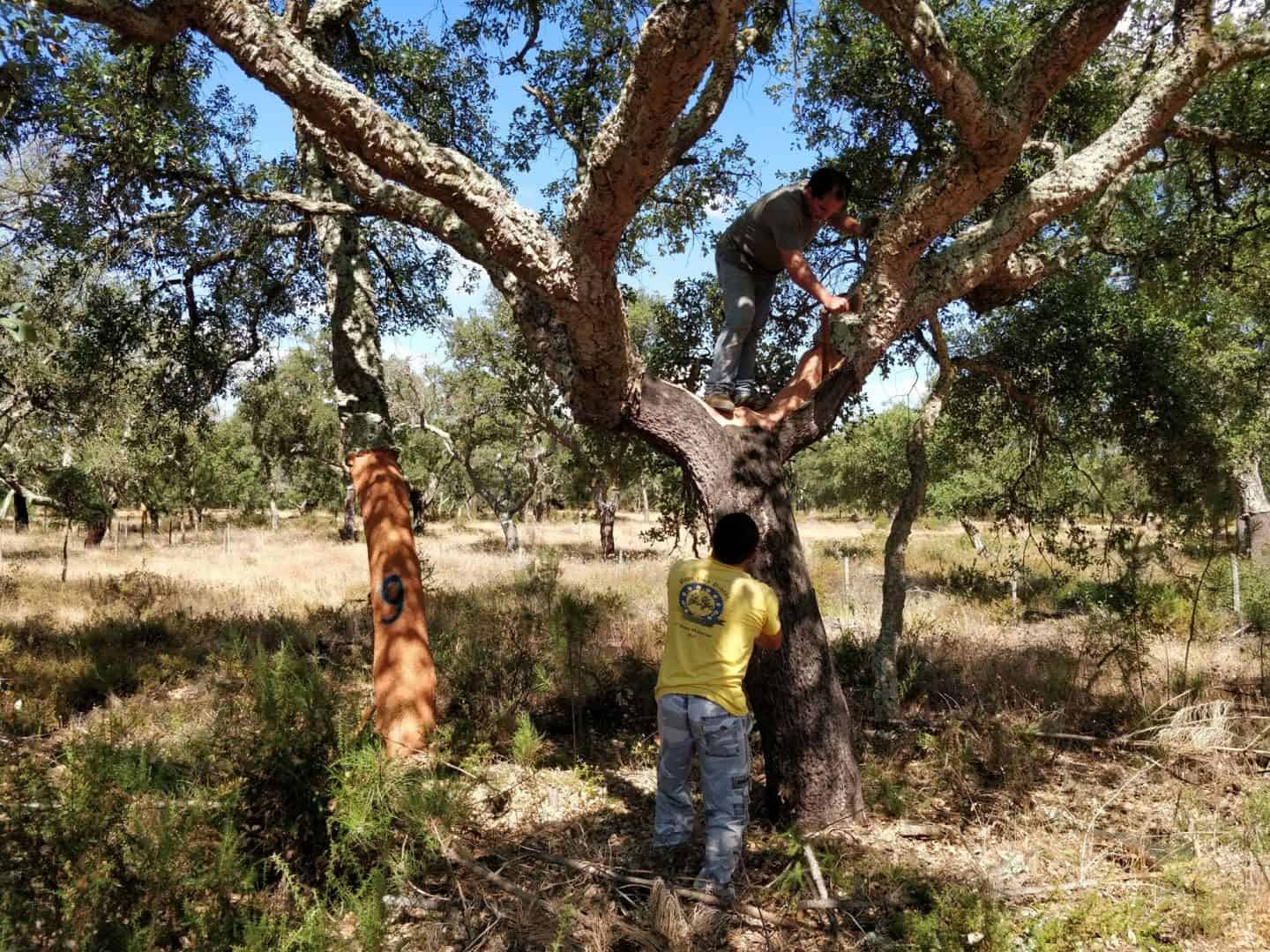
The first full day of the trip kicked off with a visit to a cork oak forest to see the men harvesting the cork. I had no idea what to expect but I was impressed with how skilled they were. Using axes, they hacked the bark from the trees, careful not to do any damage. The bark came off relatively easily and it was explained that they have to wait for the right weather conditions in order for the tree to surrender its bark.
The weather conditions also dictate where the cork oak trees grow as they are only found in the Western Mediterranean Basin (Italy, France, Spain, Portugal, Morocco, Algeria, and Tunisia). But interestingly, the cork oak forest in Portugal accounts for about 50% of the World production of cork!
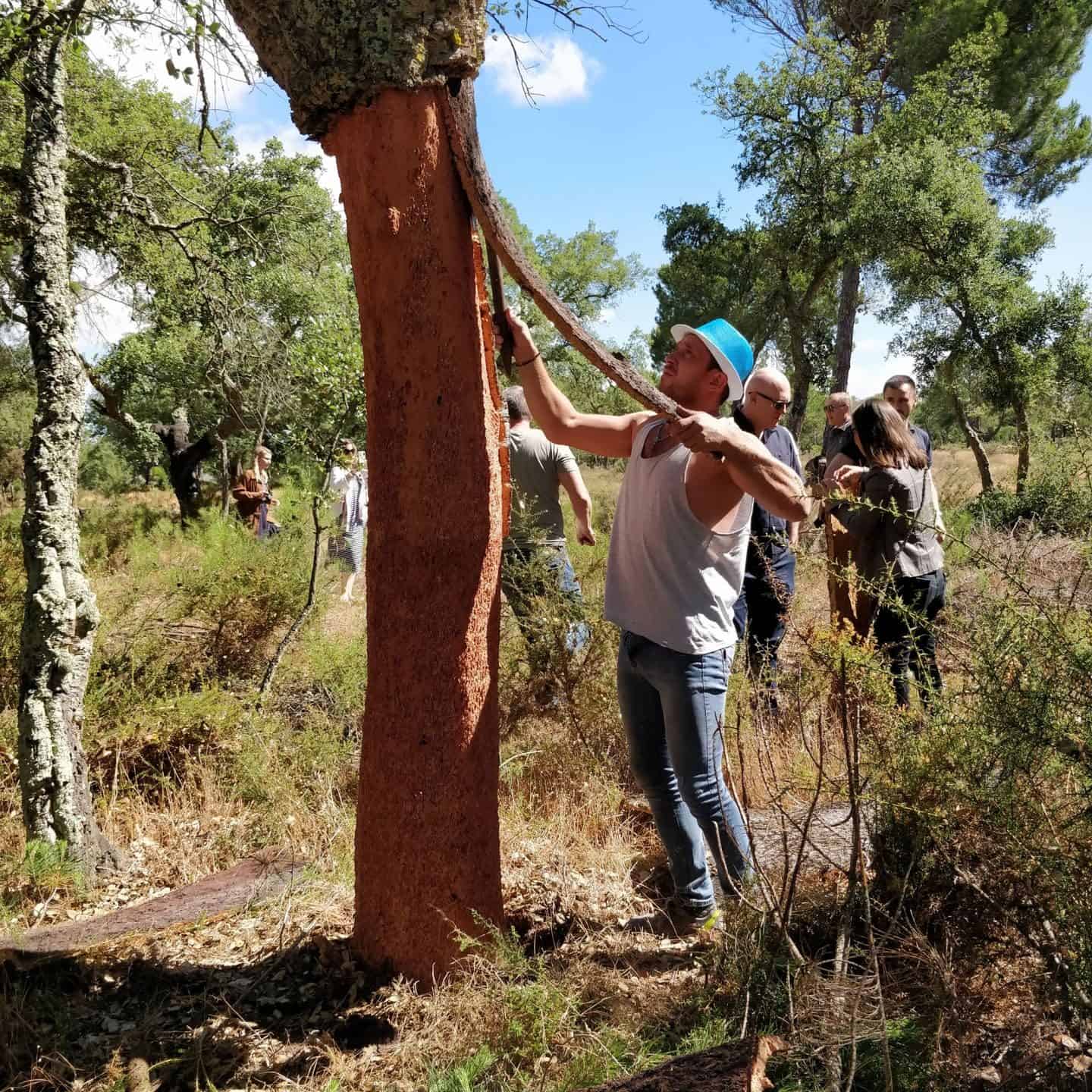
We also learnt that the forest is self-populating for the most part and that a cork oak tree can only be harvested once it reaches the ripe old age of 25 years with a trunk circumference of 70cm when measured 1.3m from the ground. After that, the harvest can be repeated every nine years as the tree needs this time to replenish its bark. Once the bark has been removed, the harvesters use spray paint to paint the last digit of the year on to the tree trunk so that they know when the tree can next be harvested.
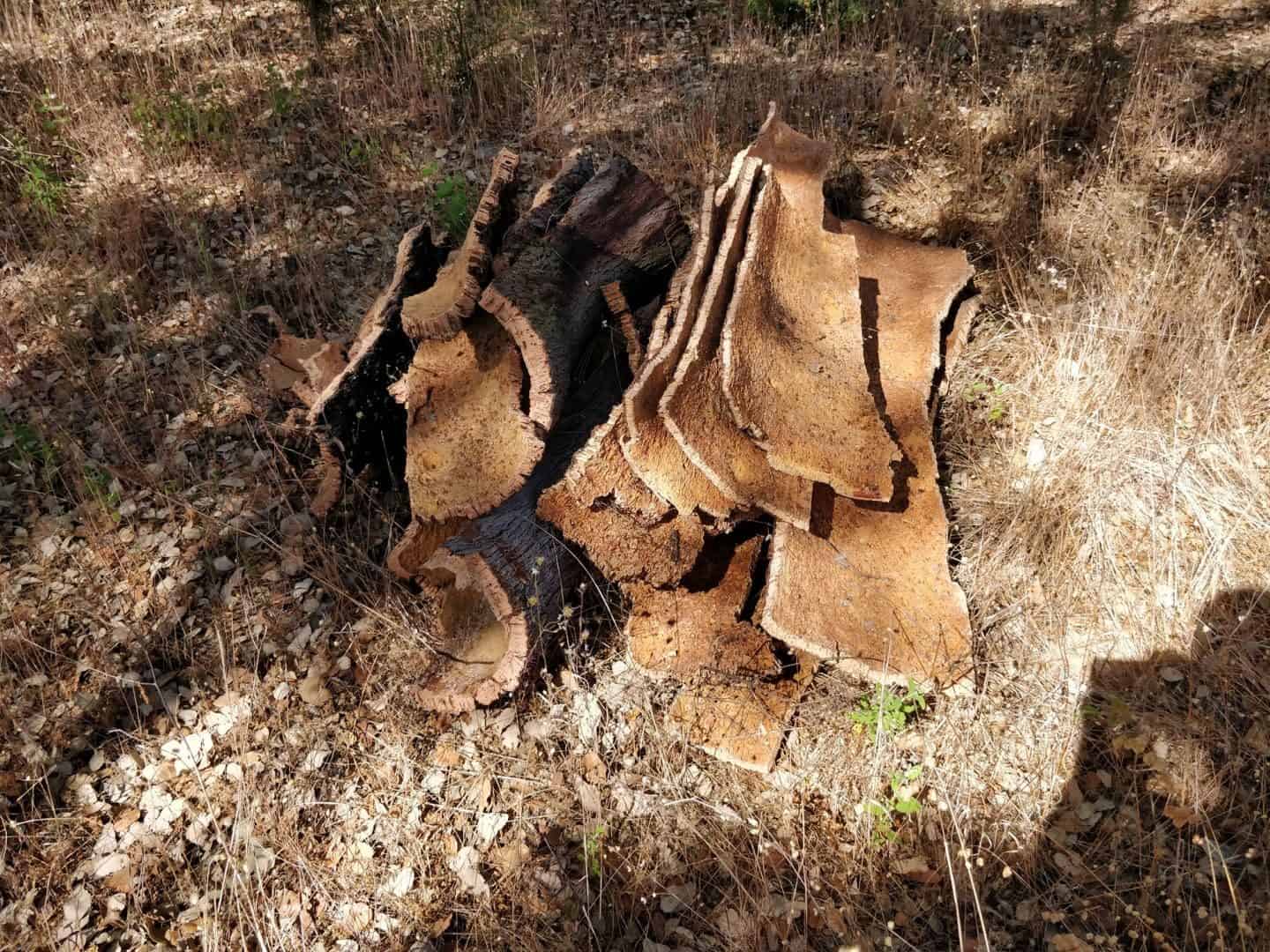
Roughly 30% of the cork that is produced by the cork oak forest is used to make wine stoppers (approximately 5.5 billion wine stoppers are sold annually), but this 30% generates 70% of the turnover of cork production. The remaining 70% of the cork produced goes into making other products like flooring and wallcoverings, furniture, building facades, insulation, surfboards, shoes, clothes, and believe it or not it is even used for aerospace applications due to its unique properties.
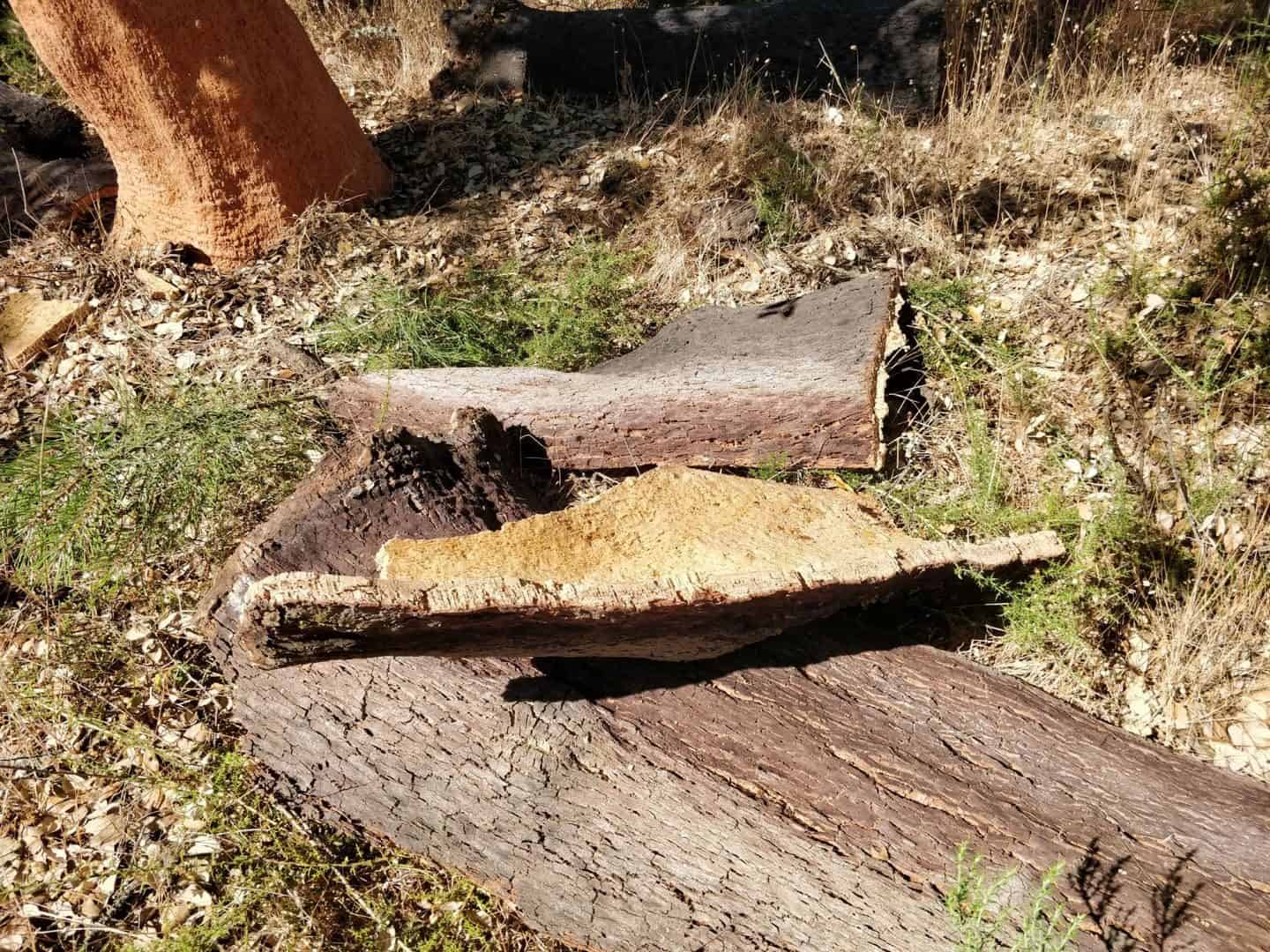
The first three harvests cannot be used to make wine stoppers as the irregular structure and extreme hardness of the cork is not suitable, so this will all be made into other products like flooring.
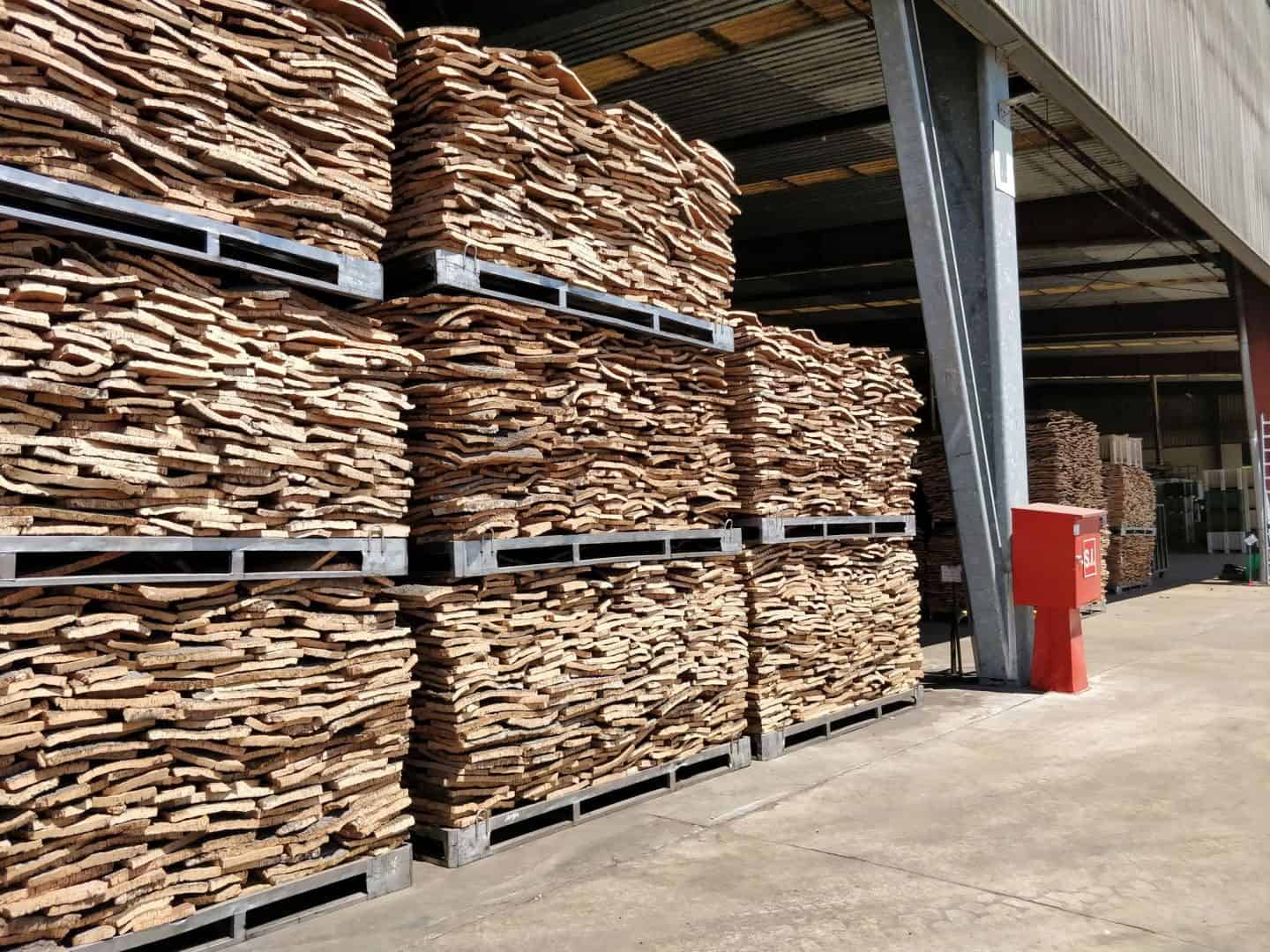
So once the cork has been harvested it is transported to the production plant to be hand sorted by thickness and quality. It is then stored outside for a minimum of six months, but usually up to a year. This is because it needs to stabilise by being exposed to the elements.
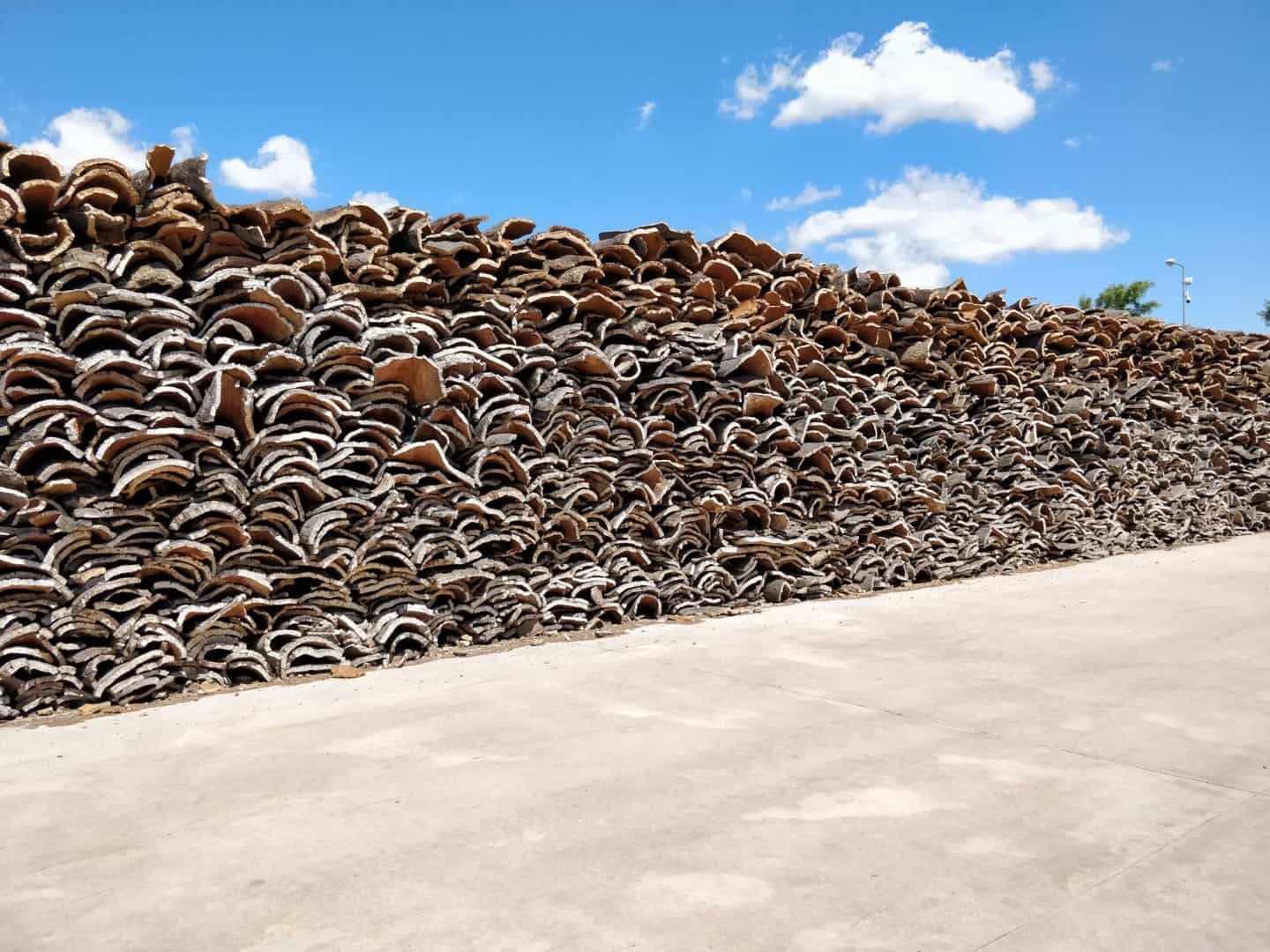
Only the very best quality cork will be used for wine stoppers and it must be boiled in hot water in order to remove any insects that may be living in it and to regulate the moisture content. This is done in huge mechanical vats that the cork is immersed in.
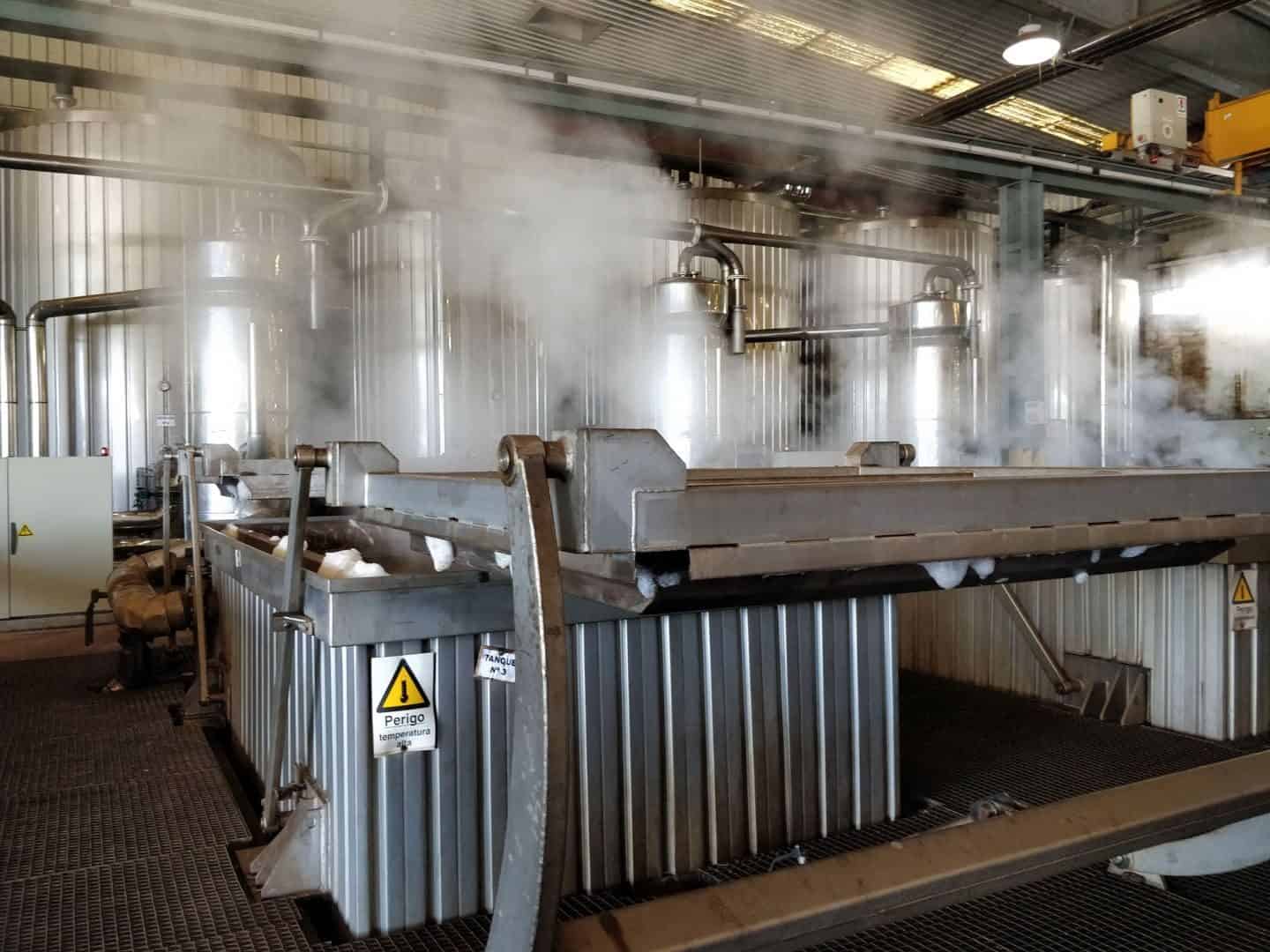
After our factory tour, where we saw how cork wine stoppers and cork flooring is made (we weren’t allowed to take photos) we got to visit the showroom and have the full cork experience. We were able to see and touch all the things that can be made from cork and to learn what makes cork the ideal material for all these different applications.
It was so interesting to learn more about cork production in terms of sustainability. I knew that the tree regenerated, but what I didn’t know is how much carbon the cork oak forest can retain. In total, the Western Mediterranean Basin has the capacity to retain approximately 30.66 million tons of C02. The carbon that is absorbed is actually stored in the cork for the entire lifetime of the product. So cork production is actually carbon positive as the process captures more carbon that it creates.
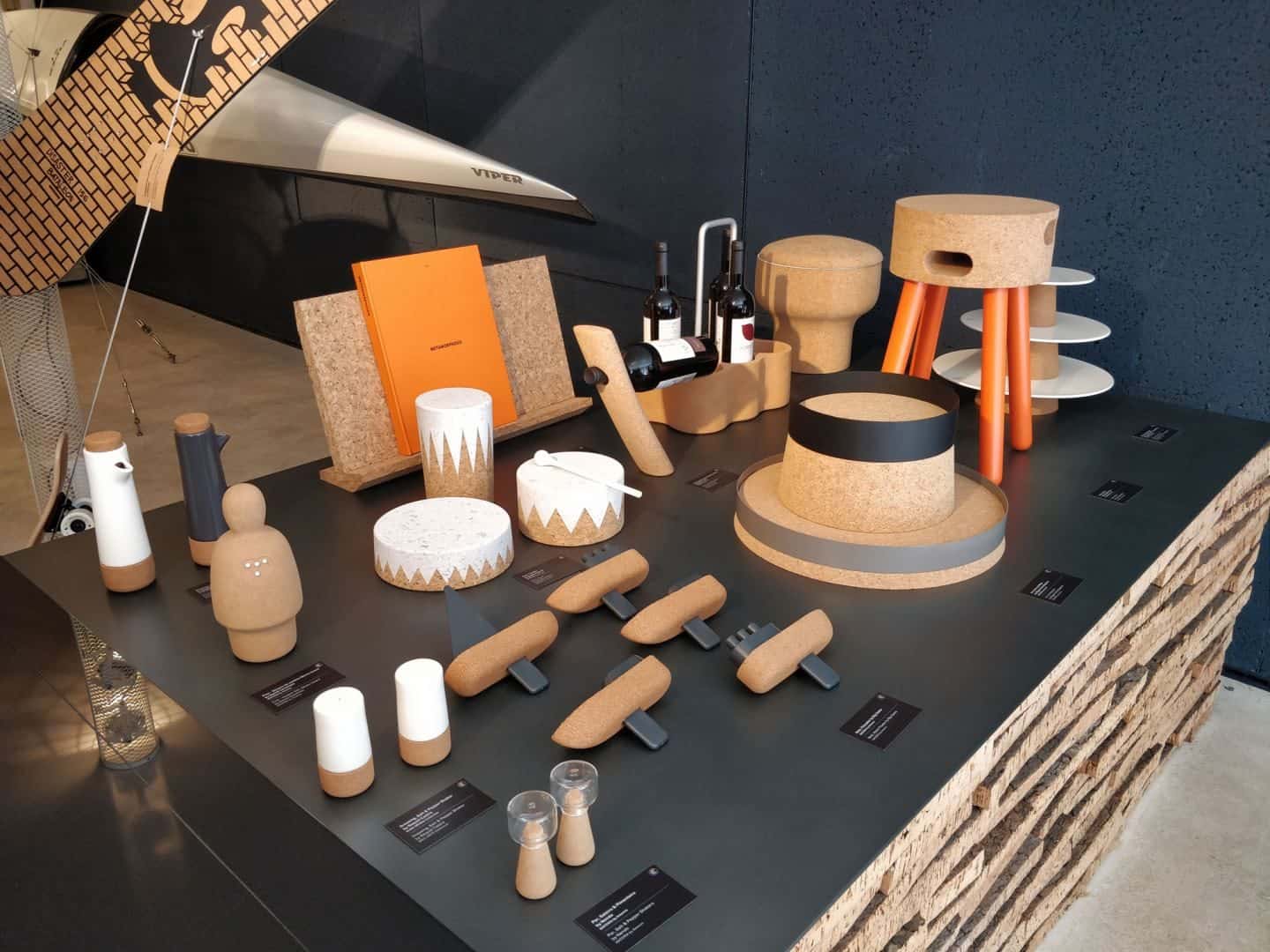
I also hadn’t realised what a circular process cork production is. I found it astounding to learn that there actually isn’t any waste throughout the whole process. The top quality cork is made into wine stoppers and everything else is ground down to be used in other applications. Even the dust from the production lines is vacuumed and conducted to silos, where it is burned to generate energy through biomass. In fact, 65% of the energy required to power the plant comes from cork dust.
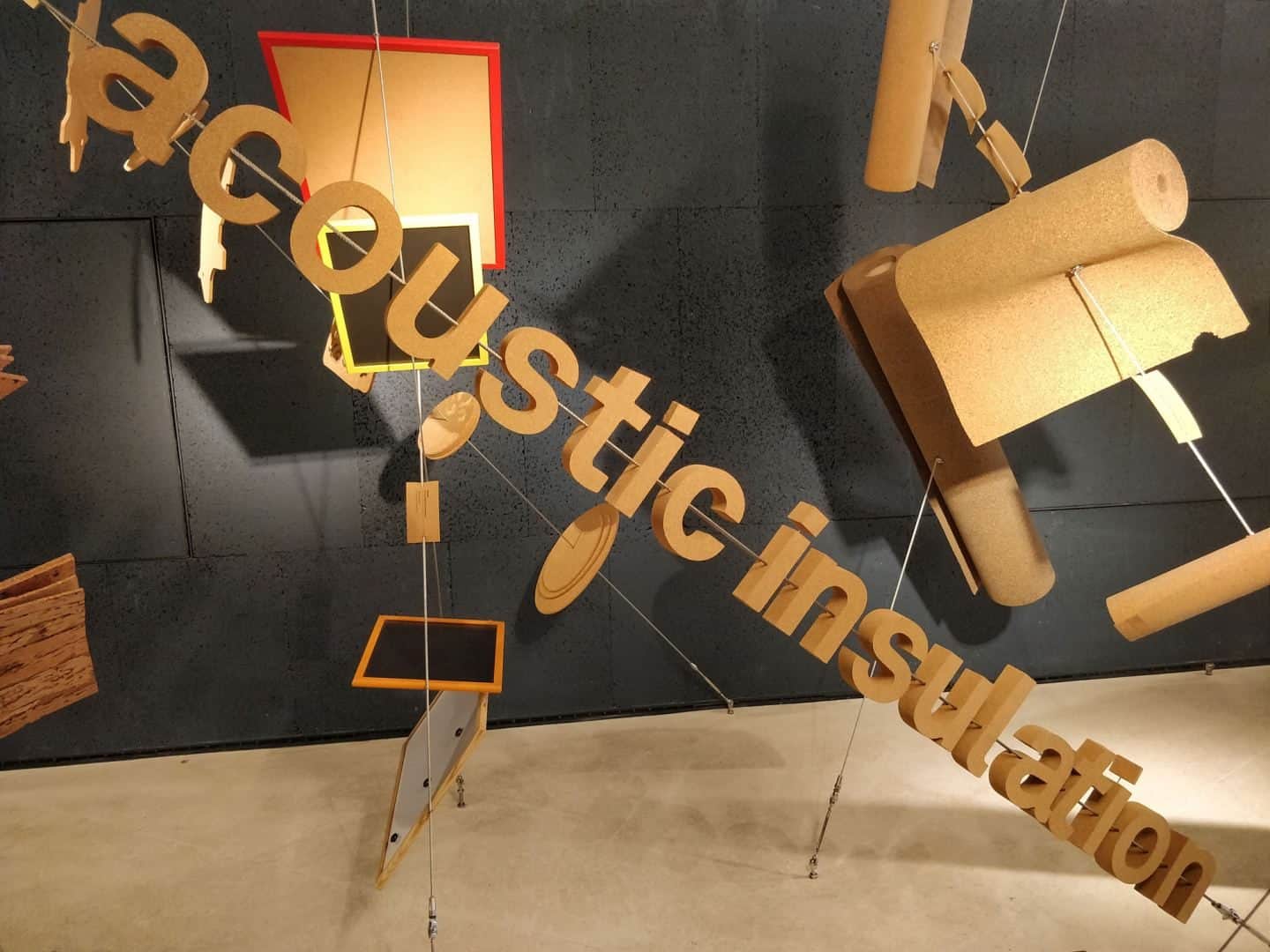
I took the liberty to make a little video of the trip so you can properly see what I got up to. Photos are nice and all, but I’d rather take you along with me so you can get a firsthand insight into everything I saw and did. I hope you enjoy it.
I will be following up this post soon with another post all about cork flooring so make sure you subscribe to my weekly newsletter so you don’t miss the post.
Also leave me some feedback below. How do you feel about cork? Did you know what a sustainable and circular product it is? Have you invested in any cork bits for your home? Would you now you know what a fabulous natural material it is?
Wow, this is absolutely beautiful. I didn’t know any of these before now. The article is very informative, thanks for sharing.
Another great Video Stacey. Really takes me back. What a lovely trip it was. x
Thanks Carole, indeed it was a lovely trip, definitely one of the most interesting press trips I’ve been on. I’m totally and utterly in love with cork now! I’ve been browsing online to see what else I can try to slip into our home past my husband. lol