Any of my friends and long-time blog readers will know that what I love most about design writing, whether that’s blogging or writing for magazines, is the story behind the projects and products that I feature. I love interviewing designers and finding out about their inspiration, their background and their journey so far. I also like looking at the behind the scenes story to see how products are designed and manufactured. I never turn down the opportunity to get the inside story! Especially when it’s a local company.
Original Style is a leading manufacturer and supplier of tiles sold by independent retailers and through their own showrooms throughout the UK. They are based an hour down the road from me in Exeter and I’ve wanted to work with them for quite some time now, ever since I saw the collaboration that they did with Kimberly of Swoonworthy on her front garden makeover. When they approached me a little while ago, I immediately asked if it would be possible to do a tile factory tour so I could see what goes on behind the scenes and how their products are developed and manufactured.
Many of their products are handmade and hand-painted or screen printed by hand on site here in Devon. So to me this was hugely exciting. Now, I know for many people this would be deathly boring and walking round a factory is certainly not a very glamorous experience, but I honestly don’t think that it’s possible to truly appreciate a product until you can understand all the time and hard work that has gone into designing and making it. Only then can you understand the true value of that piece.
Meeting the Team
So on a beautiful day in late September I drove down to Exeter to meet the Original Style team. A few of the team members were relatively new to the company so they joined me on the tour as part of their induction process. I think it’s so lovely that even those who work in more office based roles get to experience the factory tour and find out how everything is made.
After all how can you effectively sell a product that you don’t understand? We were also accompanied by Stevie, the in house photographer who took a lot of the photos that you will see in this post. Thanks Stevie!
A bit of Background
First off, I was introduced to Sylwia and Melissa who both work in PR. They gave me a brief run down of Original Style’s history, market position and client base. It is a family owned business that was set up by two childhood friends. It was created in 1986 as a division of Stovax and was originally set up to develop a range of fireplace tiles to match the cast iron fireplaces produced by Stovax.
Very quickly it became apparent that there was a demand for statement wall tiles, so Original Style developed a range of Victorian wall and floor tiles, which are still their most popular range today.
A Network of Supportive Retailers
Unlike other brands, Original Style don’t sell through chain stores. Instead, they work with a network of 600 independent retailers in the UK and 2000 globally. These retailers are chosen very carefully as it is important for Original Style that they offer a similar level of support and customer service that they themselves would provide. There are also six dedicated Showrooms in the UK where customers can go to fully experience the product range on offer.
Colour Alchemy
Once I learnt a bit about the company’s origins we headed onto the factory floor where Scott was kind enough to walk us through the whole making process. He explained that 90% of the glazes that they use are made in house and those that aren’t are made specifically for them in Stoke.
They have over 300 colours available to use in their product ranges and he explained to us how many of the colours are made and how this has changed over the years.
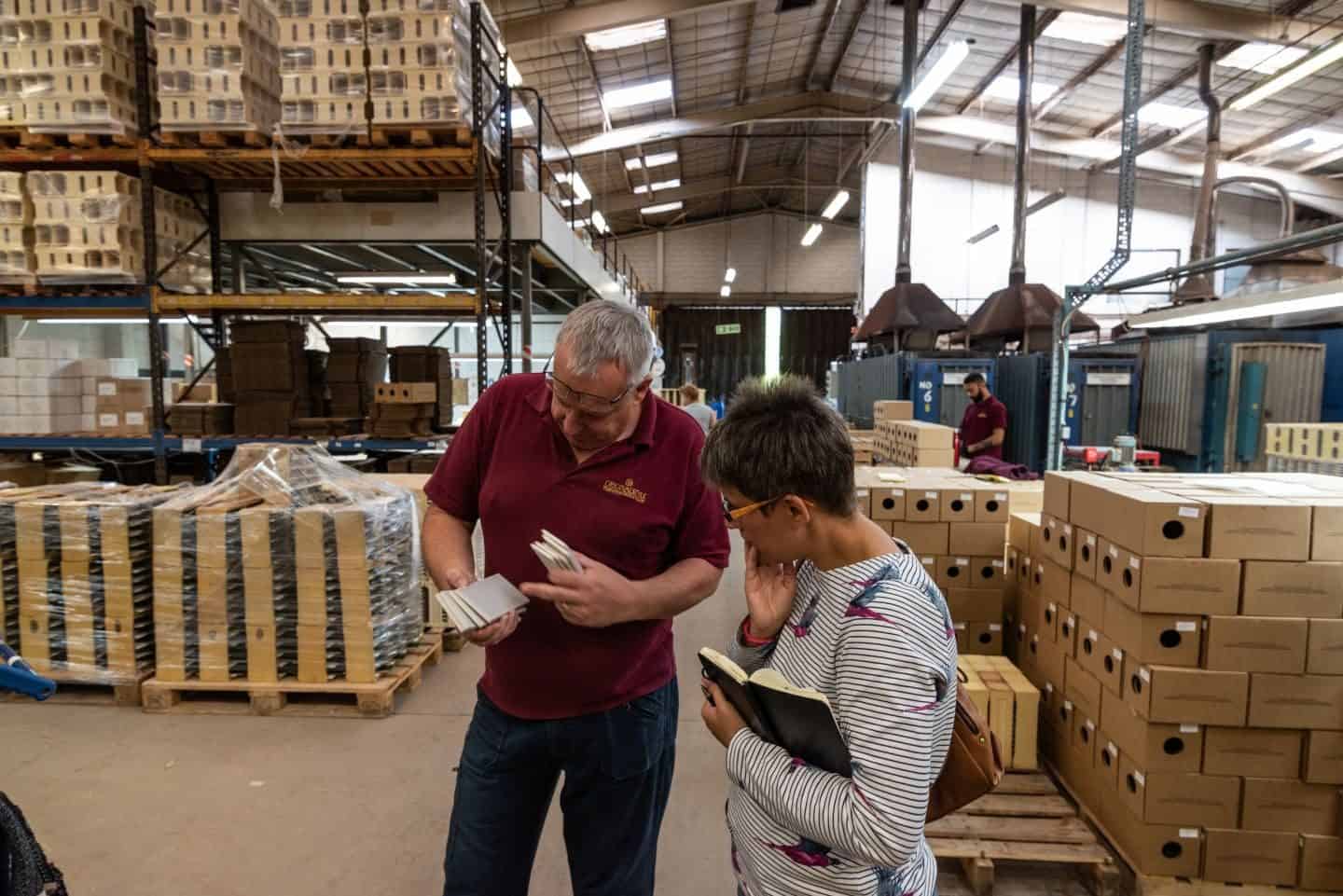
Quality Control
The factory produces between 150-180k tiles per week with roughly 138k successfully making it to the warehouse. The reason for this discrepancy is due to the super stringent quality controls that the tiles have to meet. Every single tile is inspected for flaws and unless they meet the set standards they cannot be passed for sale.
Even the slightest colour discrepancy or smallest bubble is enough for a tile to be rejected. However, many of these seconds tiles are sent by the pallet load to a tiling school so that the students can practice their tiling skills.
Fire it Up!
The tiles are fired in an enormous kiln that can hold up to 11,800 pieces at one time. The firing process takes 14 hours and the temperature is gradually raised by 150c per hour up to a maximum temperature of 1035c. It’s no wonder the tiles need to be left to cool for 36 hours before they can be removed from the kiln.
Now this lengthy process means that it’s almost impossible to get orders rushed through. No matter how urgently tiles may be required, the firing and cooling process require a set amount of time and this cannot be compromised.
Made by Hand
We were then taken to an area of the factory where tiles are made entirely by hand by a process called slip casting. This is where liquid clay, called slip, is poured into moulds, left to set and then removed once ready. The tiles, which are called biscuits before they are glazed, are then fired at 1140c.
Original Style makes all its own moulds for this process. They are therefore able to take on bespoke commissions and much smaller runs. The only limitation is the client’s budget as it is obviously more expensive to do one off items.
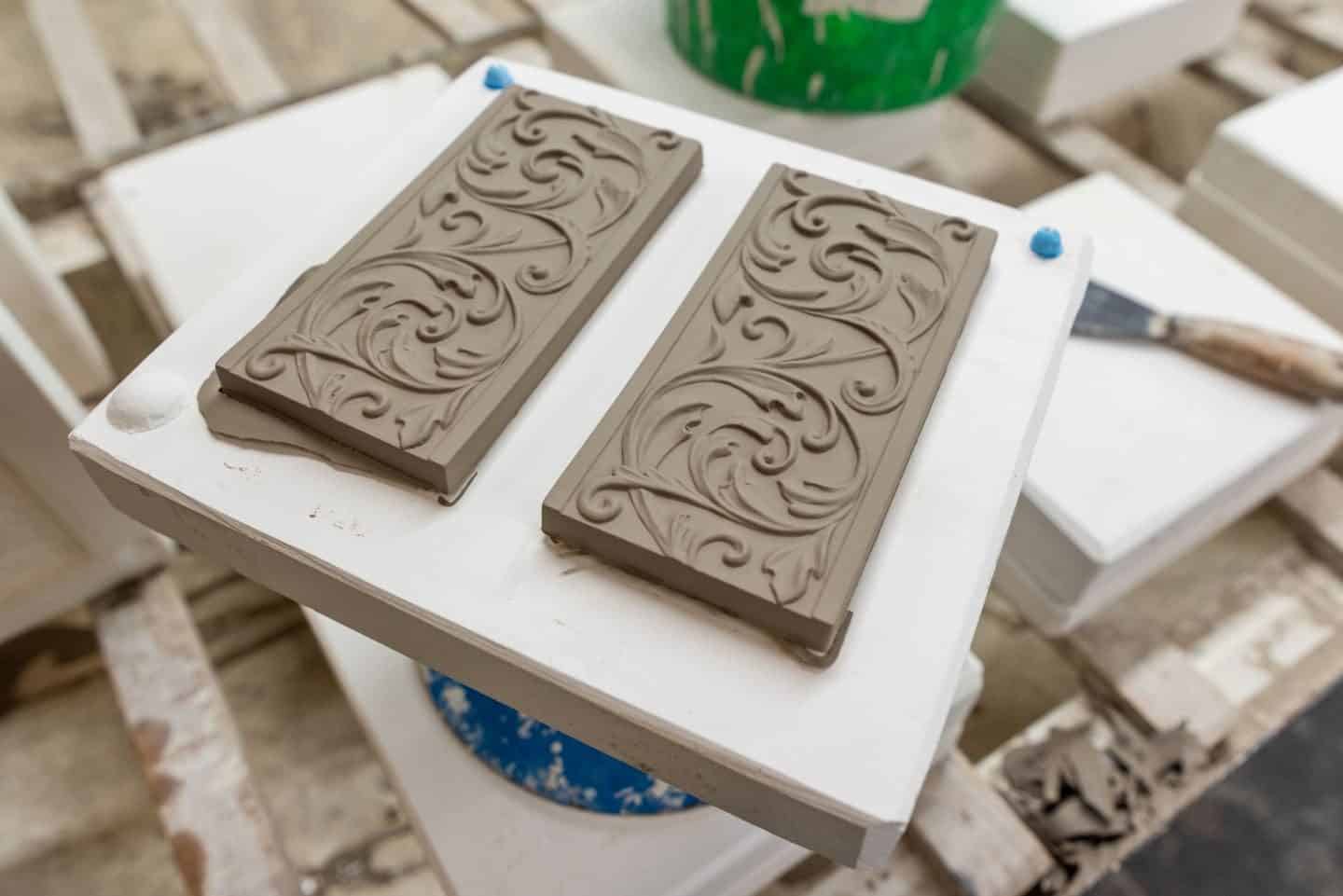
Large-Scale Projects
Many of these tiles are used for decorative border designs. However, Original Style has also worked on some really large-scale projects like the regeneration of the train station in Exeter where they created exact replicas of the original tiles helping to restore the station to its former glory.
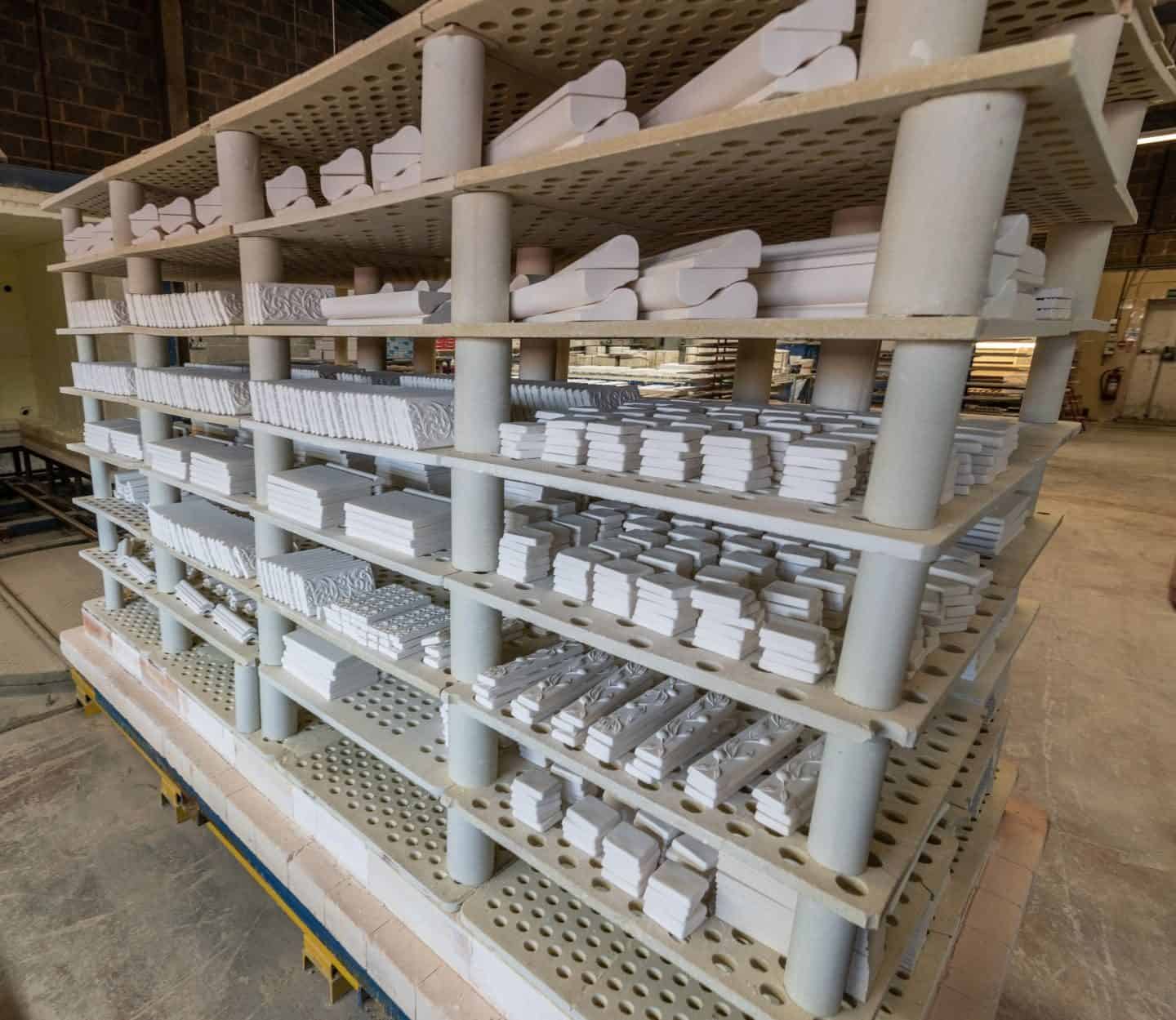
Hand-Painted
I think my favourite part of the factory tour had to be when we were able to have a go at hand painting our own tile. Under the expert guidance of Helen, we were all taught how to paint a pear tile and I can tell you now, it’s much harder than it looks.
Helen made it look a breeze of course and when I asked her how long she’d been doing it she refused to answer which spoke volumes!! She explained that Original Style has a team of outworkers who paint the tiles from home and that every one has a very distinct style so she can always tell who has painted which tile.

Digital Printing
We were also able to see Original Style’s relatively new digital printing press where their range of digitally printed tiles is created. Now producing digitally printed tiles requires nowhere near the time or effort needed to make tiles by hand, glaze them and fire them in a kiln. It’s all done by a machine of course so very little human skill goes into this process.
But I couldn’t help but swoon over all the lovely designs in Original Style’s digitally printed portfolio. I’m not a very decorative person so these muted, minimalist, geometric designs really appealed to me and I’m planning to do another post on the Living range as I was just blown away by the beauty of these tiles.
Screen Printing
The final stop on the factory tour was to see the screen printing process. I’ve always wanted to try screen printing but I assumed that when I did it would be on fabric. In all honesty, I didn’t even know that tiles could be screen printed. We met Helen (a different Helen) who is one of two ladies responsible for the screen printing.
She showed us a selection of tiles that she had been printing and explained how difficult it is to get everything lined up. I had a go at printing my own tile but I didn’t quite apply the right pressure so there were parts where the ink didn’t come through as well as it should. But for a first try I was happy with my efforts.
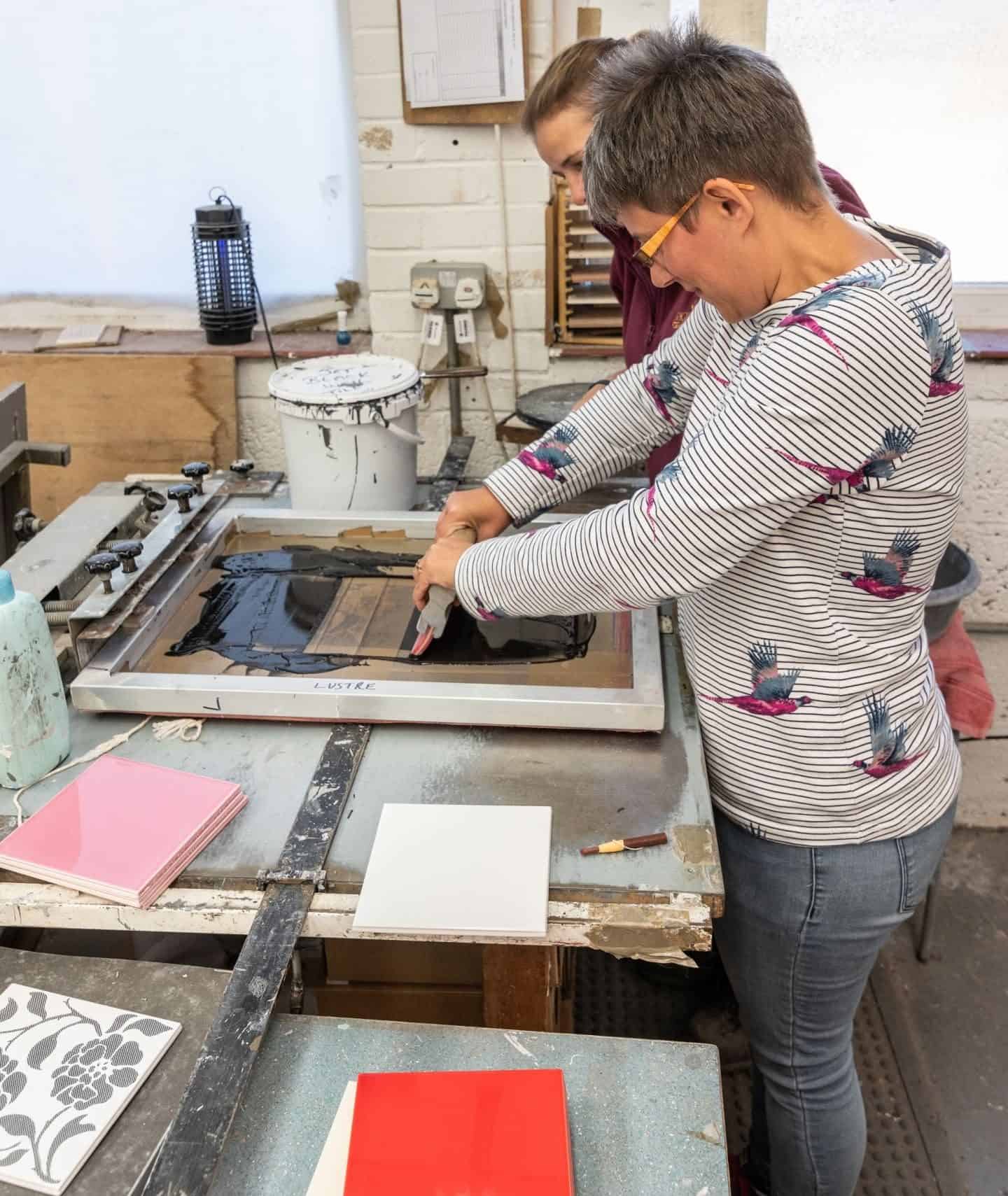
Just before we finished up for the day, I got to have a quick look in the design studio. It was a really inspiring space. A huge array of tiles lined the walls and on one side of the room was an enormous real life Pinterest board.
One of the team was in Bologna at the time at Cersaie, a huge international exhibition of ceramic tile and bathroom furnishings. I would have loved to have been a fly on the wall for the follow up discussions about the trends that were spotted. But luckily, fellow blogger and design writer Mary Middleton of Hello Peagreen shared her findings from the show here.
So that was my tour of the Original Style tile factory. It was such a lovely day and I really appreciated the team taking the time out to explain to me in detail how everything works and what the different processes are. It was a real pleasure to see tiles being made, painted, printed and adorned with transfers by hand. And whilst digitally printed tiles may be having a bit of a moment, you just can’t underestimate the time, effort, craftsmanship and years of experience that go into these tiles.
You just can’t beat a behind the scenes tour to get to know a company and you’ve done an amazing job Stacey! I adore Original Style’s tiles and have featured them over on my blog. And how great are they that they offer imperfect tiles to the tiling school!! Great post! And huge congratulations on your Amara win – so very well deserved!!!
This is a wonderful behind the scenes. My favourite part was that the company sends all ‘seconds’ to a tiling school. So instead of throwing away, they provide material for the new generation of tilers, hurray!
Yes I loved that too! When I heard about how many tiles get rejected I was wondered about the environmental impact, but this is a lovely way to make use of them.
Sounds like you had a great time Stacey. It was really interesting to read the process of creating tiles. I would love to have a go at the hand painting!
It was actually really therapeutic Lin. I enjoyed my little hand-painting session.
Great post! and I could not agree more….a good back story always ensures heightened appreciation.
I am a firm believer in this. The more I know about a company the more loyal I become and the more I appreciate the value they create!
Fabulous post! I think its great that you share the story behind the brand it is fascinating to hear about the stringent selection process and to know what goes on with the rejected tiles. Love that they then go on to get used for learning! Love it xxx
Yes this was a lovely bit of information to find out! It’s the kind of thing you’d never know without digging that little bit deeper!
What a fascinating insight, Stacey, it looks like you had a great day. The tile painting looks fun – do we get to see your finished tile?
Ha, perhaps I’ll post it on insta Rachel!
Looks like you had a fun day out. I love seeing a behinds the scenes on a brand, big or small, you feel so much more connected to the product. Lovely post Stacey.
Thanks Jen. I’m so glad it’s not just me who enjoys looking behind the scenes!
Oh how interesting to find out more about what goes on behind the scenes. I never knew how they were made and that there are so many different ways to make a tile! We have a new Orginal Style showroom coming to our area and I can’t wait to visit it!
Oh that’s so exciting! If you do visit, make sure you check out the Living Range. It’s stunning!
What a great day out – so good to get hands on like that! I find it so fascinating to go behind the scenes and discover the many processes that go into making these beautiful end products. Thanks for sharing! X
I’m a big fan of Original Style. This is a lovely insight into their factory and story :-)
Thanks Carole!
So much fun!! We’ve used this brand before too! Have a great weekend x
It was such a fun day!
It’s all so impressive, isn’t it? Goodness, the amount of work for the fired tiles is incredible and I didn’t know you could screen print tiles either! Fascinating look behind the curtain of a company I really like too (having first-hand experience!) :) PS. I am now missing my beautiful front garden tiles! Ha! Thanks for the shout out lovely! xxx
Pleasure! That was such a stunning transformation and ever since I saw it on your blog I have wanted to do something to spruce up the entrance to our flat. But it’s difficult to know what to do with so many steps up to the flat. Don’t want to make it a slippery death trap!